Clean rooms, as we know them today, are specialized facilities designed to maintain an extremely clean environment to protect products, processes, or experiments from contamination. They are used in a variety of industries, including pharmaceuticals, electronics, aerospace, and medical devices. The history of clean rooms can be traced back to the early 20th century when the concept of a clean environment was first introduced in the medical industry.
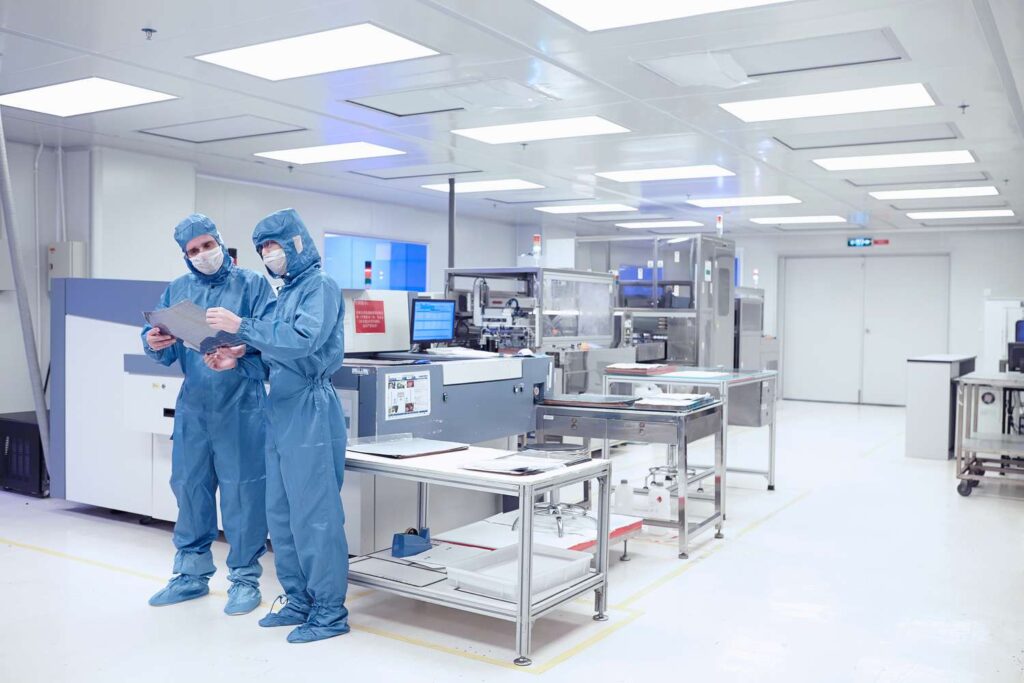
One of the earliest known examples of a clean room was created by the Lister Brothers, a British manufacturer of surgical instruments, in the early 1900s. They had noticed that many of the surgical instruments they manufactured were being contaminated during the manufacturing process, leading to infections in patients. To solve this problem, they created a room with smooth, non-porous walls and floors, which could be easily cleaned and disinfected. They also installed filters to control the airflow and prevent dust and other contaminants from entering the room.

The use of clean rooms expanded during World War II when they were used to manufacture specialized equipment for the war effort, such as lenses and radar components. In 1949, the US National Bureau of Standards (now the National Institute of Standards and Technology, or NIST) established a clean room for research in semiconductor technology. The creation of this clean room marked the beginning of the use of clean rooms in the electronics industry.
In the 1950s and 1960s, the aerospace industry began to use clean rooms to manufacture spacecraft and launch vehicles. NASA’s first clean room was built in 1961 to assemble the first manned spaceflight, Project Mercury. The clean room was equipped with a laminar flow system, which directs filtered air in a constant stream to minimize the buildup of airborne contaminants.

In the 1970s and 1980s, the pharmaceutical industry began to use clean rooms to manufacture drugs. The creation of the US Food and Drug Administration’s (FDA) current Good Manufacturing Practices (cGMP) regulations in 1978 helped to standardize the use of clean rooms in the pharmaceutical industry. These regulations require pharmaceutical companies to have a clean environment to ensure the safety and efficacy of their products.
Today, clean rooms are used in a wide range of industries, from food production to nanotechnology. They are critical for manufacturing products that require a controlled environment to ensure their safety and quality. The design and operation of a clean room are essential to prevent contamination, which could lead to product recalls, costly production delays, and harm to public health.
Clean rooms are classified according to their level of cleanliness, which is determined by the number of particles per cubic meter of air. The classification system ranges from ISO Class 1 (the most stringent) to ISO Class 9 (the least stringent). ISO Class 1 clean rooms are used for the most sensitive applications, such as semiconductor manufacturing, while ISO Class 9 clean rooms are used for less sensitive applications, such as packaging and labeling.
Clean Spaces was developed to be able to store all your cleanroom data (Cleaning, Disinfecting, Particle Counting, Micro Counting, Audit Logs, and Historical Charts/Graphs) in one central location to provide evidence of compliance. Gone will be the days of paper and pen, ink and toner costs, expensive equipment, and lost paperwork. We are a simple, elegant solution that is sure to save your company a HUGE amount of waste and expenses by digitizing the work you have to do anyway.
The history of clean rooms shows how they have evolved from a solution to a medical problem to a critical component of modern manufacturing. Today, clean rooms are used in a wide range of industries to ensure the safety and quality of products. The development of clean rooms has been driven by the need for increasingly clean environments to manufacture increasingly sensitive products, and this trend is likely to continue as new technologies emerge. As industries continue to rely on clean rooms, it will be essential to maintain high standards of cleanliness and to continually innovate to meet the evolving needs of manufacturing. And now, with Clean Spaces, you can keep track of all of your clean room data with the click of a button!
Don’t forget to get in touch and stay tuned for our latest updates!