The design of a clean room is an incredibly crucial element for meeting the desired sanitation classification(s) for every single industry that utilizes clean rooms. The walls, floors, doors, and airflow materials and technologies are essential to maintaining a controlled environment, which is necessary for pharmaceuticals, electronics, aerospace, medical devices, and so on.
The key design features of a clean room include the layout, materials, HVAC system, and air filtration system. Let’s take a closer look at each of these design features and how they work together to maintain a controlled environment.
Layout
The layout of a clean room is critical to ensure that products, processes, or experiments are protected from contamination. A clean room’s layout should minimize the number of entry and exit points and ensure that there is no cross-contamination between different areas within the clean room.
So, step into the extraordinary world of a clean room, where precision meets purity and innovation thrives under pristine conditions. The structure and layout of this technological haven are meticulously designed to ward off even the tiniest particles. The walls, crafted with the utmost care, are made of non-shedding materials like stainless steel or fiberglass, ensuring a sterile environment. The floors, resistant to static electricity, boast epoxy or vinyl finishes, facilitating easy cleaning and preventing the buildup of dust.
Every corner of the room is guarded by air-tight doors, equipped with high-efficiency filters to maintain an immaculate atmosphere within. Windows, if present, feature multiple layers of transparent polycarbonate, serving as the gateway to a world beyond while upholding the uncompromising standards of cleanliness. These structural components, carefully assembled, collaborate harmoniously to create an oasis of purity, safeguarding delicate processes and scientific breakthroughs from the clutches of contamination.
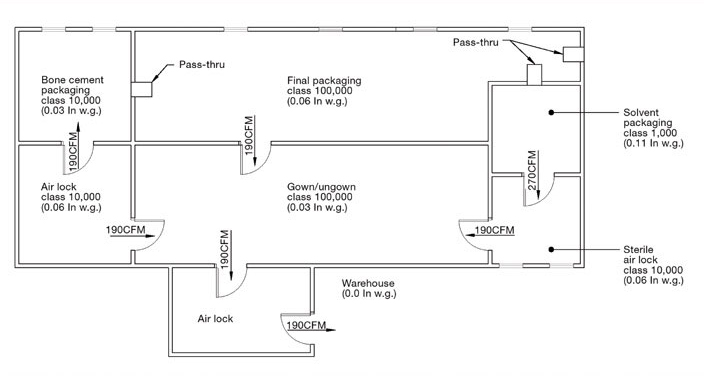
Materials
The materials used in a clean room should be smooth, non-porous, and easy to clean. Walls, ceilings, and floors should be made of materials that do not shed particles, such as stainless steel or vinyl. The materials used in a clean room should also be resistant to chemicals and disinfectants used for cleaning. Some of the most common materials are as follows:
- Stainless Steel: This gleaming marvel graces the walls, ceilings, and floors of a clean room, ensuring a pristine environment. Its smooth, non-porous surface resists particle shedding, effortlessly deflecting the tiniest intruders. With an inherent resistance to chemicals and disinfectants, stainless steel stands as a stalwart guardian against contamination, preserving the sanctity of scientific endeavors.
- Vinyl: Vinyl possesses an irresistible charm. Its non-shedding nature and smooth, seamless finish create a seamless expanse where cleanliness thrives. Resistant to chemicals and disinfectants, vinyl unveils a world where scientific progress takes center stage.
- Polycarbonate: Although not many clean rooms foster a lot of windows, if any at all, those that do are usually made of polycarbonate. Polycarbonate’s multifaceted layers form an unyielding barrier against impurities, ensuring a clear, distortion-free view. Resistant to chemicals and disinfectants, polycarbonate allows the light of knowledge to illuminate the scientific wonders that unfold within.
- Epoxy: In the alchemy of clean room flooring, epoxy weaves its magic. Its seamless, glossy finish enthralls the eye while offering unrivaled durability. This chemical and disinfectant-resistant material resists static electricity, preventing the accumulation of dust and protecting the delicate processes from within the clean room.
- Non-Porous Materials: These extraordinary materials resist the infiltration of contaminants. They create a fortress of cleanliness, ensuring a pristine environment where scientific breakthroughs can flourish. These non-porous wonders include laminates, fiberglass, and specialized coatings, each with its own unique properties.
HVAC System
The HVAC system in a clean room is designed to maintain a controlled environment by controlling temperature, humidity, and airflow. The HVAC system should ensure that the temperature and humidity are within the specified range, and the airflow is directed in a specific direction to minimize the movement of particles within the clean room.
Air Filtration System
The air filtration system in a clean room is essential to maintain a controlled environment. The air filtration system should remove particles from the air making sure they reside within the specified range. The air filtration system should include a pre-filter to remove larger particles and a HEPA filter to remove smaller particles.
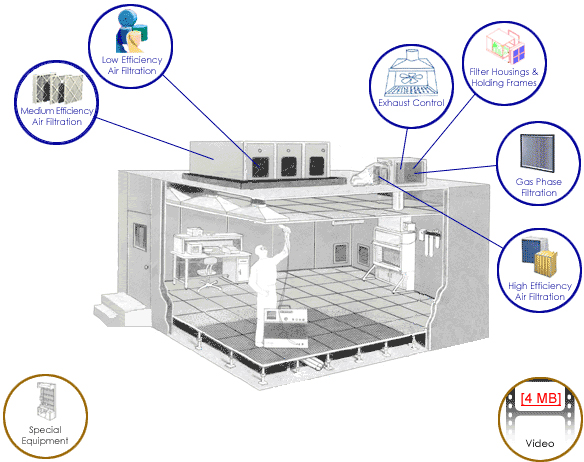
The HVAC system and the air filtration system work together to maintain a positive pressure differential within the clean room. A positive pressure differential means that the pressure inside the clean room is higher than the pressure outside the clean room. This pressure differential prevents particles from entering the clean room through gaps in the walls or doors.
The design of a clean room must be validated and monitored to ensure that it meets the specified cleanliness requirements. Validation involves testing the clean room’s design and operation to ensure that it meets the specified requirements. Monitoring involves regular testing of the clean room to ensure that it continues to meet the specified requirements.
The design of a clean room is critical to maintaining a controlled environment necessary for many industries. The key design features of a clean room include the layout, materials, HVAC system, and air filtration system, each working together to create the perfect environment.